UNDERSTANDING
LEMO AND FISCHER PUSH PULL CONNECTORS
LATCH DESIGN
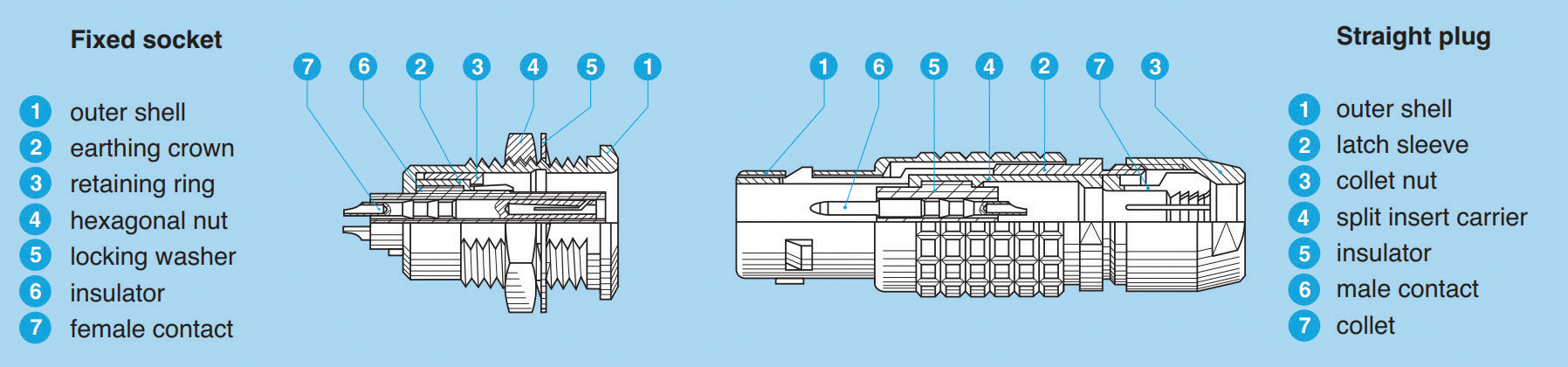
Figure 1: Lemo B-series cross section: Lemo Unipole Multipole catalog page 13
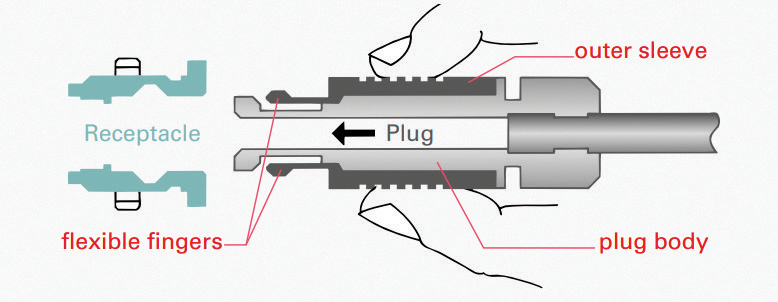
Figure 2: Fischer latch design: Fischer Technical Specification Volume 1 page A-5.
INGRESS PROTECTION
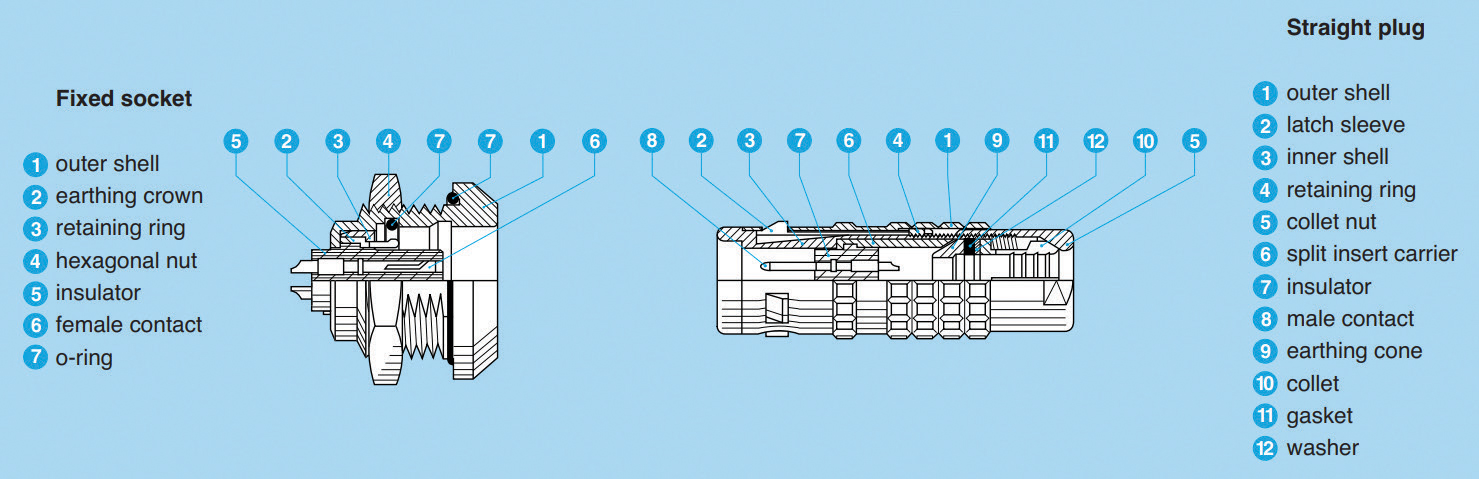
Figure 3: Lemo K-series cross section: Lemo Unipole Multipole catalog page 38
INGRESS PROTECTION
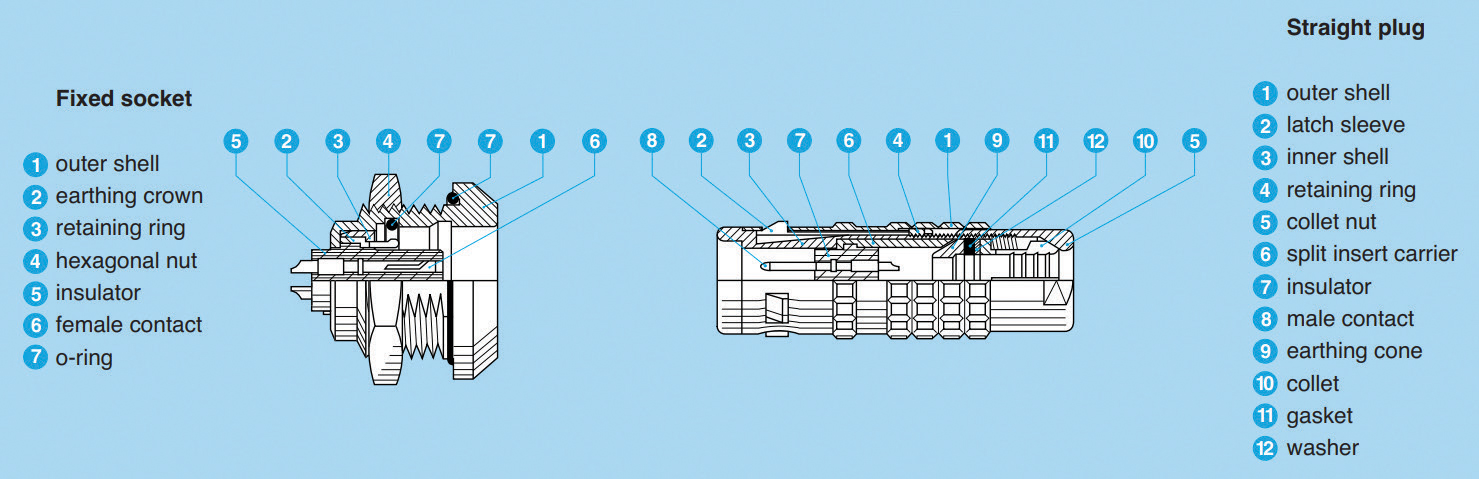
Figure 3: Lemo K-series cross section: Lemo Unipole Multipole catalog page 38
SHELL SIZES
CONNECTOR MARKETPLACE
Over the years many competitors to Lemo and Fischer have surfaced. One of the most well-known companies is ODU Connectors. ODU has backward-compatible connectors to both Lemo and Fischer. The list goes on and on, there are hundreds of companies that have simply copied the designs and offered them at a lower price. At Global Interconnect our engineers strive to innovate, not imitate. Our Purpose-Built™ connectors focus on simplified designs while maintaining quality and backwards compatibility with the industries push pull connectors. Our engineers work to understand your application and create a Purpose-Built™ solution for you, we don’t just select the closest match from a catalog. To learn more about how our connector solutions may be able to help you, check out Understanding Custom Medical Connectors.